Laser cutting is a precise and efficient method widely used in various industries to cut materials such as metals, plastics, and wood. This technology relies on a high-powered laser to make accurate cuts, providing clean edges and intricate designs. The type of gas used in the laser cutting process can significantly impact the quality and efficiency of the cut.
Using nitrogen generator in laser cutting offers several advantages over other gases like oxygen. Nitrogen prevents oxidation, resulting in cleaner cuts with no discoloration or burnt edges. This is particularly important for industries where the aesthetic quality of the cut edge is crucial, such as in the production of stainless steel and aluminum components. For businesses looking to improve their cutting processes, investing in a nitrogen generator for laser cutting can be a game-changer, ensuring a consistent supply of high-purity gas.
How Laser Cutting Works
Laser cutting involves directing a high-powered laser beam at the material to be cut. The laser melts, burns, or vaporizes the material, creating a cut. The process typically requires an assist gas, which blows away the molten material from the cut area, helping to achieve a cleaner edge. The choice of assist gas can affect the cut quality, speed, and overall efficiency of the process.
Benefits of Using Nitrogen in Laser Cutting
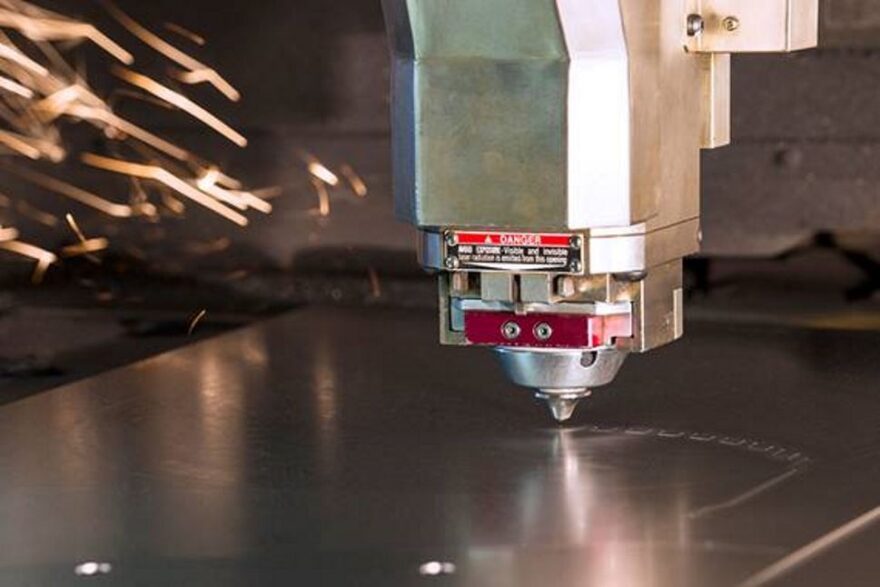
- Cleaner Cuts: Using an inert gas prevents oxidation, which can cause discoloration and rough edges. This results in cleaner, more aesthetically pleasing cuts.
- Improved Edge Quality: This method ensures that the cut edges remain smooth and free of burrs, reducing the need for post-processing.
- Faster Cutting Speeds: This gas can increase cutting speeds, particularly when working with thinner materials. This can lead to higher productivity and lower operating costs.
- Enhanced Material Properties: It helps maintain the material’s inherent properties by preventing oxidation and thermal distortion, which can weaken the material.
Nitrogen Generator for Laser Cutting
A nitrogen generator for laser cutting is an essential piece of equipment for any business looking to optimize its cutting process. These generators produce high-purity gas on-site, eliminating the need for cylinder deliveries and reducing operational costs. The generator works by separating nitrogen from the air, using either pressure swing adsorption (PSA) or membrane technology.
Investing in a generator offers several benefits:
- Cost Savings: On-site generation can be more cost-effective than purchasing and storing gas cylinders. This can lead to significant savings over time.
- Continuous Supply: A generator ensures a constant and reliable supply of gas, reducing downtime and improving productivity.
- Environmental Benefits: Generating gas on-site reduces the carbon footprint associated with the transportation and storage of cylinders.
Applications of Laser Cutting with Nitrogen

This method is used in various industries due to its numerous benefits. Some of the key applications include:
- Metal Fabrication: The gas is widely used in the metal fabrication industry for cutting stainless steel, aluminum, and other non-ferrous metals. The clean cuts and smooth edges are ideal for creating high-quality metal components.
- Automotive Industry: In the automotive sector, this method is used to produce precise components with minimal post-processing. This helps improve production efficiency and product quality.
- Aerospace Industry: The aerospace industry relies on this technique for producing parts that require high precision and durability. The process ensures that the material properties are maintained, which is critical for aerospace applications.
- Electronics Industry: This method is used to produce intricate components for electronic devices, where precision and clean cuts are essential.
Factors to Consider When Using Nitrogen for Laser Cutting
When using this gas in laser cutting, several factors need to be considered to ensure optimal results:
- Material Type and Thickness: The type and thickness of the material being cut will impact the choice of laser settings and the required gas pressure.
- Laser Power: The power of the laser will affect the cutting speed and quality. Higher-powered lasers can cut through thicker materials more efficiently.
- Gas Pressure: The pressure of the gas can impact the quality of the cut. Higher pressure can help achieve cleaner cuts, particularly for thicker materials.
- Nozzle Design: The design of the nozzle used in the laser cutter can influence the flow of gas and the overall cut quality. Using the appropriate nozzle design can help achieve optimal results.
Maintenance and Safety Considerations
Proper maintenance and safety practices are crucial when using this gas for laser cutting:
- Regular Maintenance: Regular maintenance of the generator and laser cutting equipment is essential to ensure consistent performance and longevity. This includes checking for leaks, replacing filters, and ensuring the generator is operating within the manufacturer’s specifications.
- Safety Precautions: This gas is inert, but it can displace oxygen in enclosed spaces, leading to asphyxiation hazards. Proper ventilation and monitoring of oxygen levels in the workspace are important safety measures.
- Training: Ensuring that operators are properly trained in the use of generators and laser cutting equipment is essential for maintaining a safe and efficient work environment.
Choosing the Right Nitrogen Generator
Selecting the right generator for laser cutting involves considering several factors:
- Flow Rate Requirements: The required flow rate of the gas depends on the laser cutting application. High-powered lasers and thicker materials generally require higher flow rates.
- Purity Levels: The purity of the gas can affect the quality of the cut. Most laser cutting applications require high-purity gas, typically 99.99% or higher.
- Generator Technology: Generators use either pressure swing adsorption (PSA) or membrane technology. PSA systems are generally more efficient and provide higher purity levels, while membrane systems are more compact and easier to maintain.
- Cost and Maintenance: The initial cost and ongoing maintenance of the generator should be considered. While PSA systems may have higher initial costs, they often provide lower long-term operating costs.
Future Trends in Laser Cutting with Nitrogen
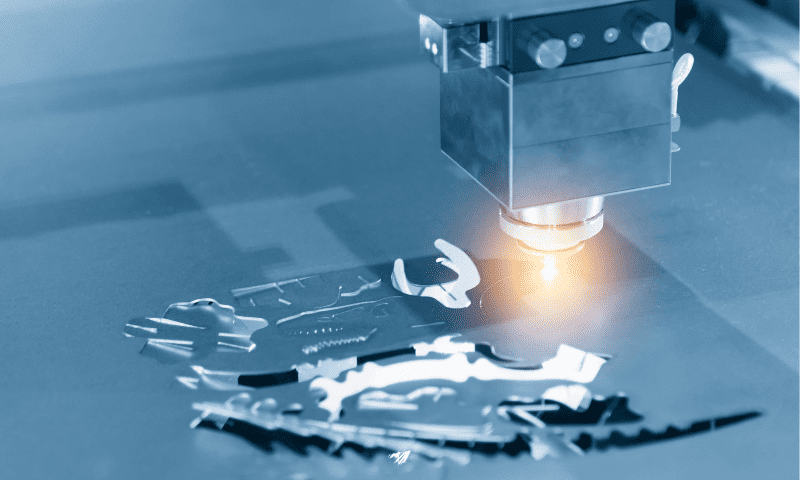
The laser cutting industry continues to evolve, with new technologies and innovations emerging to improve efficiency and quality. Some of the future trends in this field include:
- Automation: Increasing automation in laser cutting processes can improve productivity and reduce human error. Automated systems can optimize the use of gas, ensuring consistent and efficient cutting.
- Advanced Laser Technologies: Innovations in laser technology, such as fiber lasers, are improving the speed and precision of laser cutting. These advancements can enhance the benefits of using nitrogen as an assist gas.
- Sustainability: There is a growing focus on sustainability in the manufacturing industry. Using generators for on-site gas production reduces the environmental impact associated with transporting and storing cylinders.
- Integration with IoT: Integrating laser cutting systems with the Internet of Things (IoT) can provide real-time monitoring and optimization of the cutting process. This can lead to more efficient use of gas and improved cutting performance.
Conclusion
Laser cutting with nitrogen offers numerous advantages, including cleaner cuts, improved edge quality, and faster cutting speeds. Investing in a generator for laser cutting can lead to significant cost savings, a continuous supply of high-purity gas, and environmental benefits. By considering factors such as material type, laser power, and gas pressure, businesses can optimize their laser cutting processes and achieve superior results. Proper maintenance and safety practices are crucial to ensure the longevity and efficiency of the equipment, making laser cutting with this method a valuable asset for various industries. As technology continues to advance, the use of this gas in laser cutting is expected to become even more efficient and sustainable, driving further improvements in manufacturing processes.
Related Posts:
- 15 Best Gas Grills Under 300 2024 - Propane Grills…
- 20 Best Gaming Headset Under 50$ 2024 - for PC, PS4,…
- 12 Best Car Wax For Black Cars 2024 - Protection and…
- Top 16 Best Office Chair Covers 2024 - Chair…
- Top 10 Best Paint Sprayer For Cabinets 2024 -…
- Top 10 Best Outdoor Basketball Shoes 2024 - Durable…